This past week I had the privilege of doing preventative maintenance on the Dykstraflex camera for the Academy of Motion Picture Arts and Sciences. I serve on the Academy’s Technology and History Subcommittee, and following the restoration of the Dykstraflex camera crane, subcommittee members were concerned that the camera may have developed problems after having been in storage for so long. So, being a Star Wars fan, and having worked with many of the people who shot Episodes IV, V, and VI, I was thrilled to be asked to examine and conserve this extraordinary piece of film history.
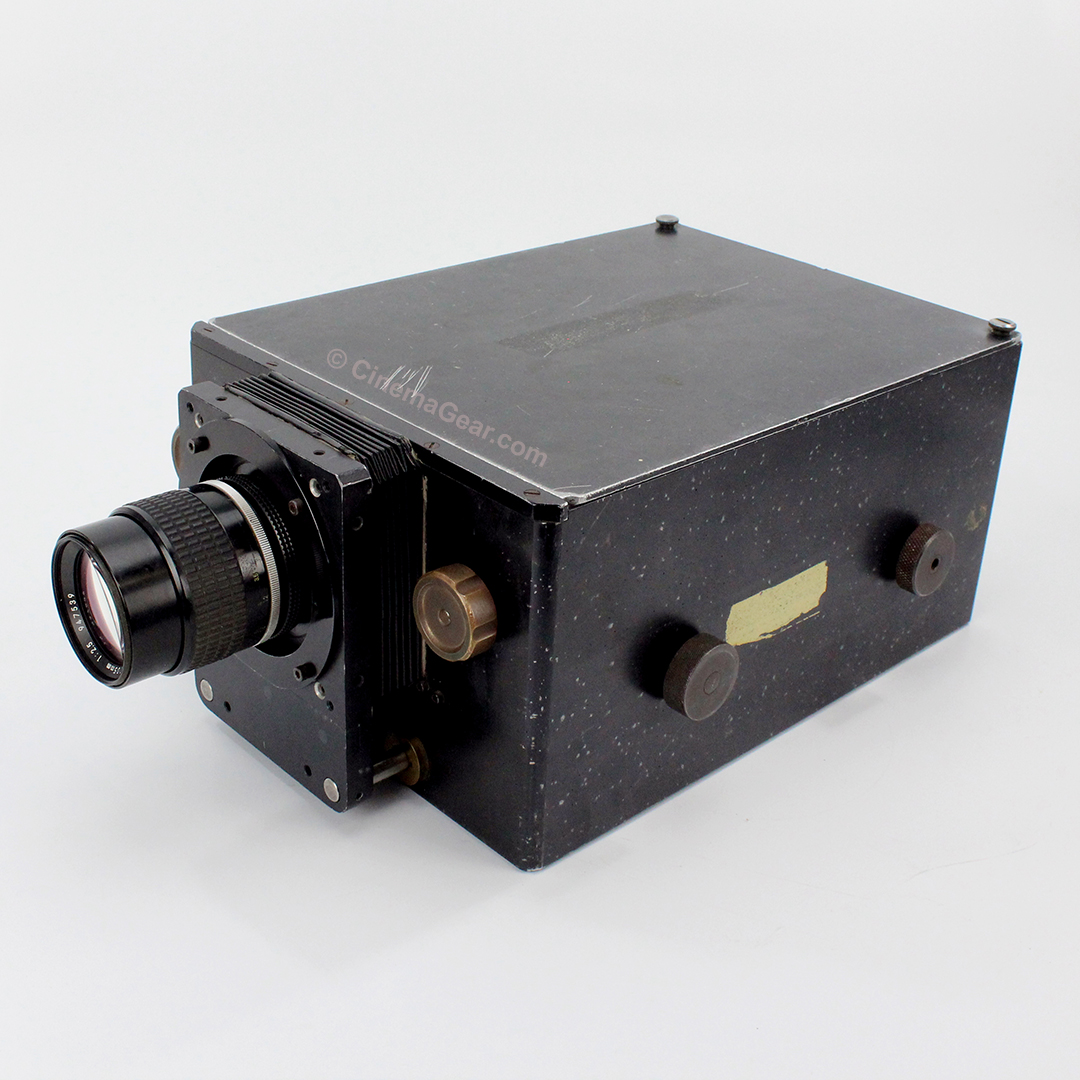
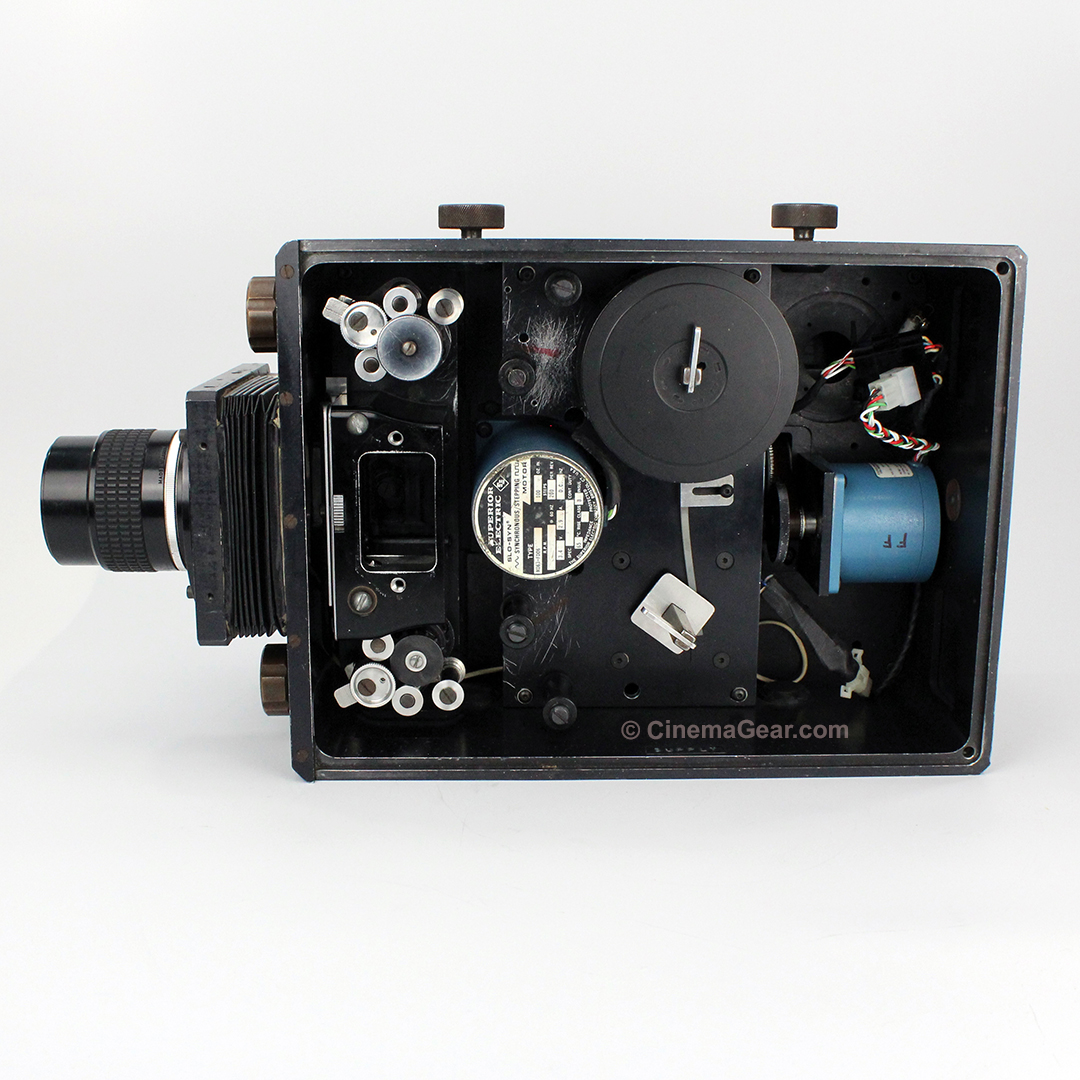
When discussing the camera with the subcommittee, my concerns were that there might be rust or corrosion on some of the moving parts, the various drive belts may have rotted or failed, that the capping shutter might have seized, and that we might find rot on the bellows. To begin servicing the camera, I first removed all of the outside covers to see if there were any glaring problems inside. Not seeing anything obvious, I removed the movement. Fortunately, even though everything was dry and all of the lubrication was crusty, there was no rust or other damage to the movement. I pulled all of the moving parts off of the movement, cleaned them in the ultrasonic cleaner, re-lubricated everything, put the movement back together, and checked the timing.
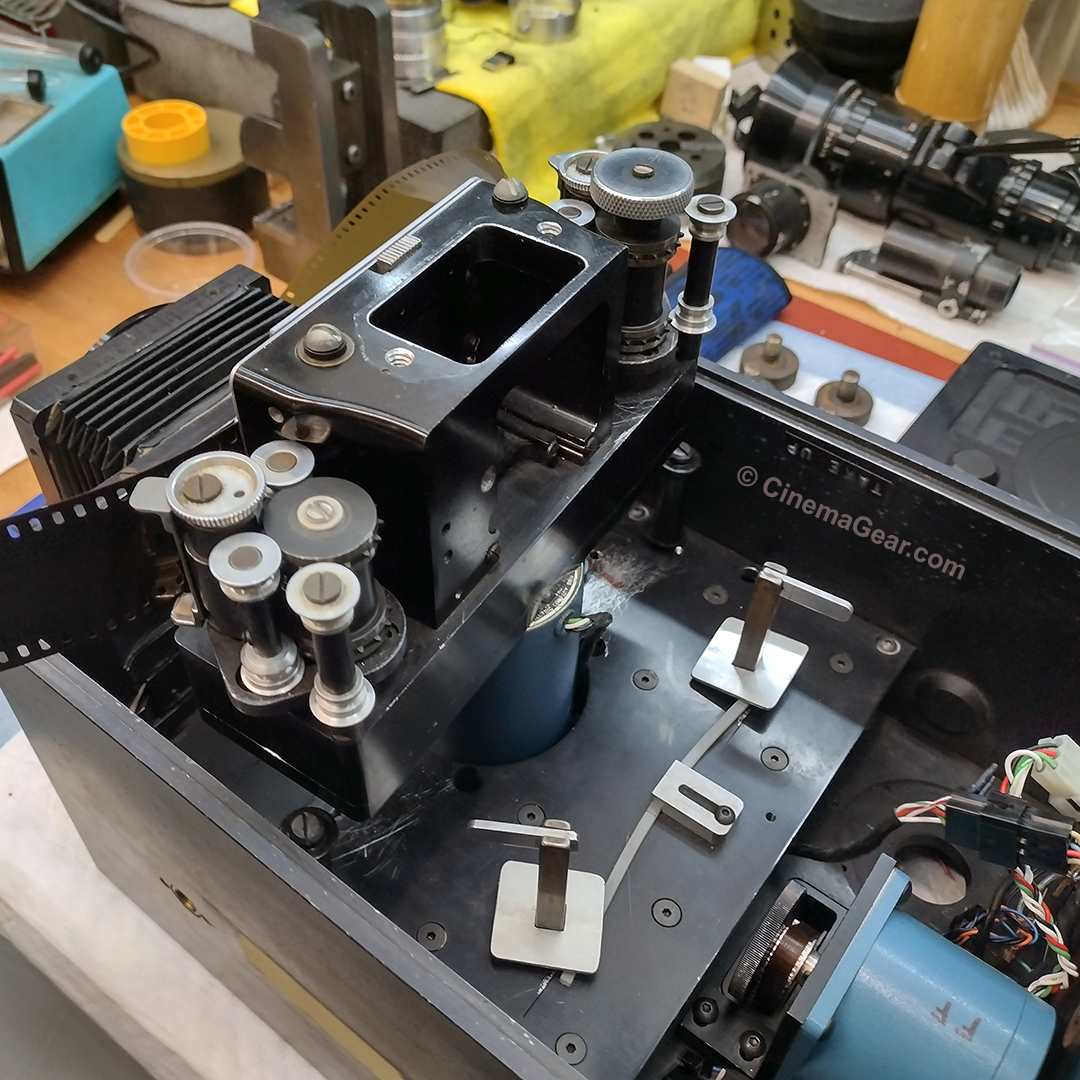
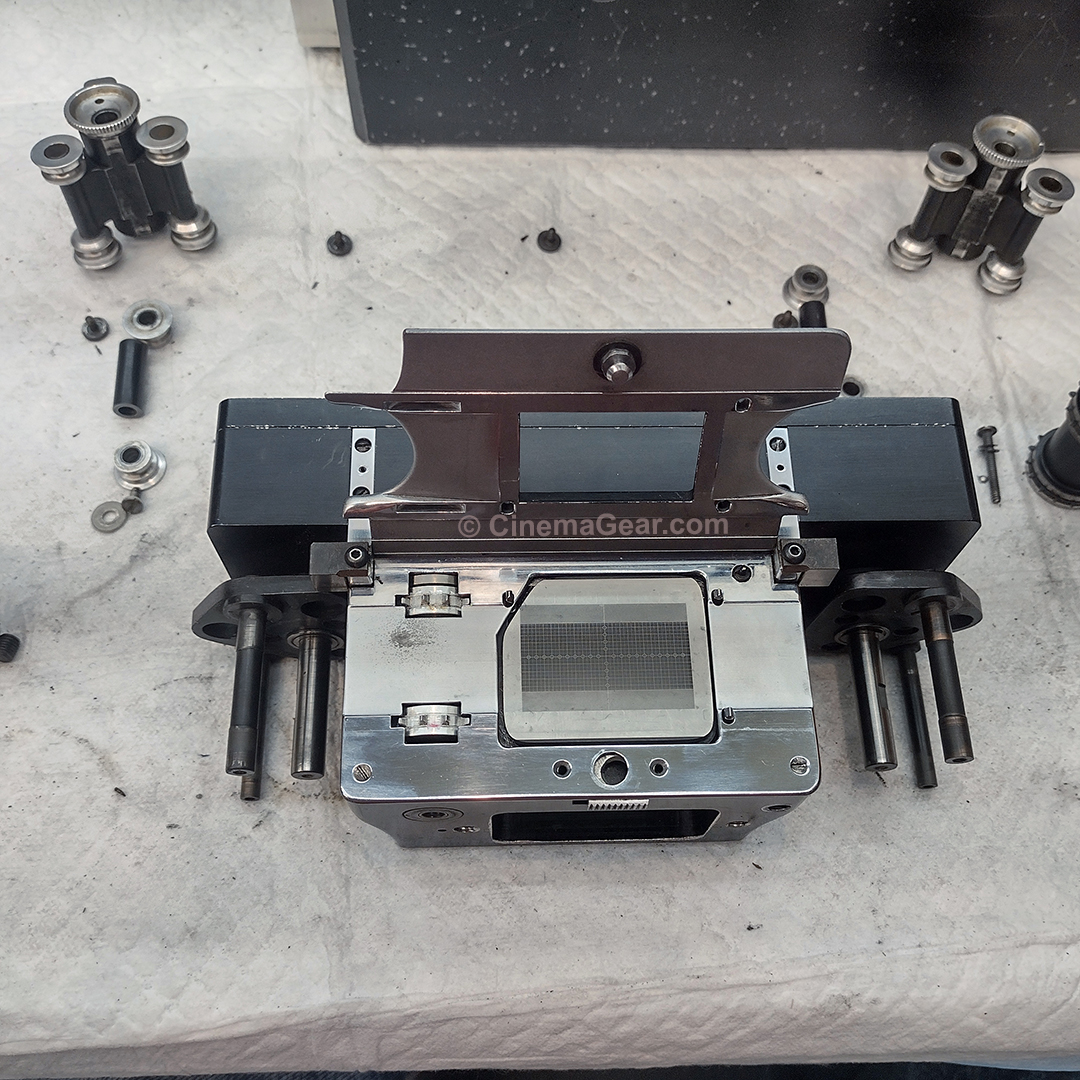
Next I removed both of the belts and inspected them, checked them with a durometer, and inspected them under a microscope to see if there was any shredding or teeth missing. Amazingly, both belts were in like-new condition, so I reinstalled them. I then moved on to cleaning and lubricating the follow focus mechanism, checked out the condition of the capping shutter, repaired the Nikon lens mount, cleaned and preserved the bellows, and put everything back together.
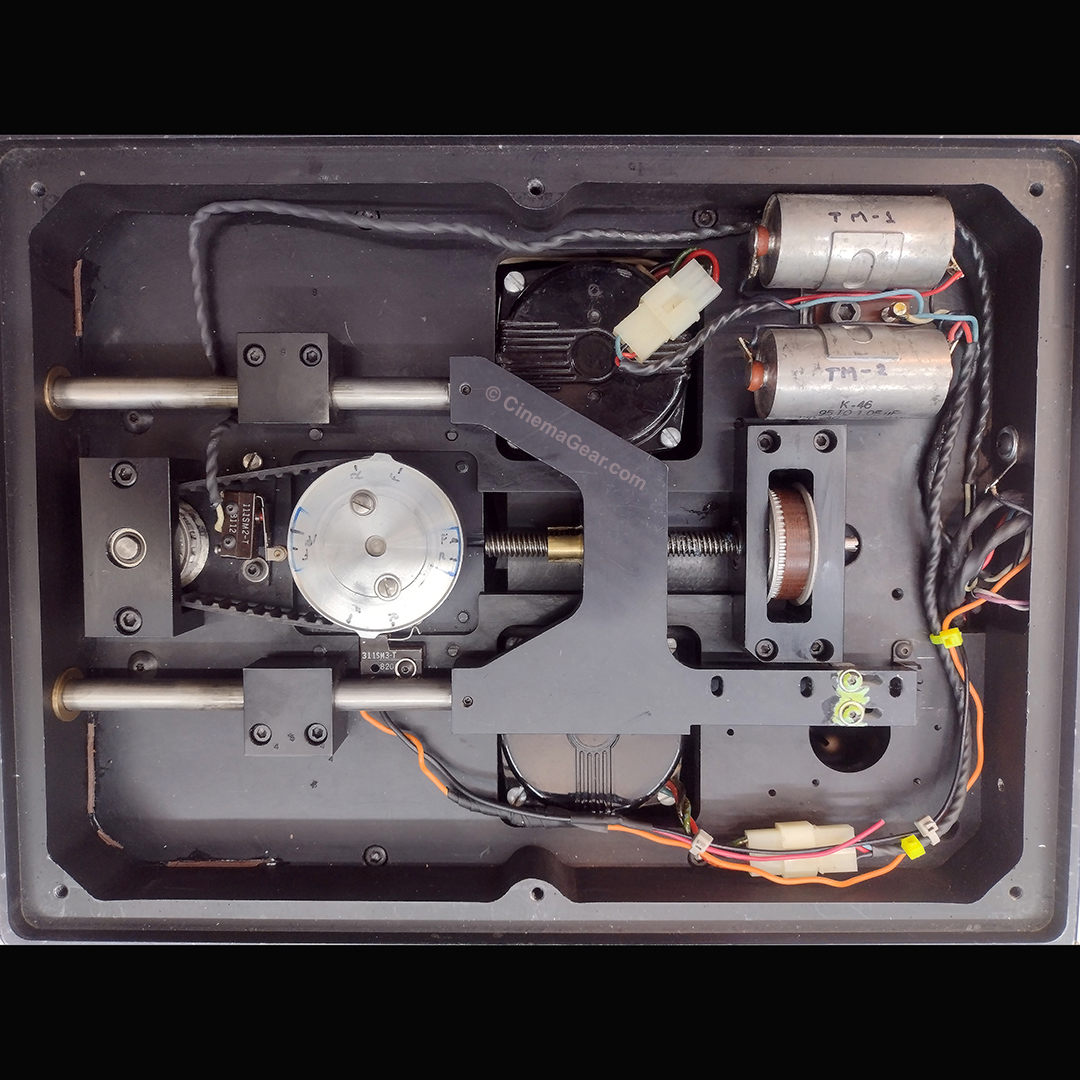
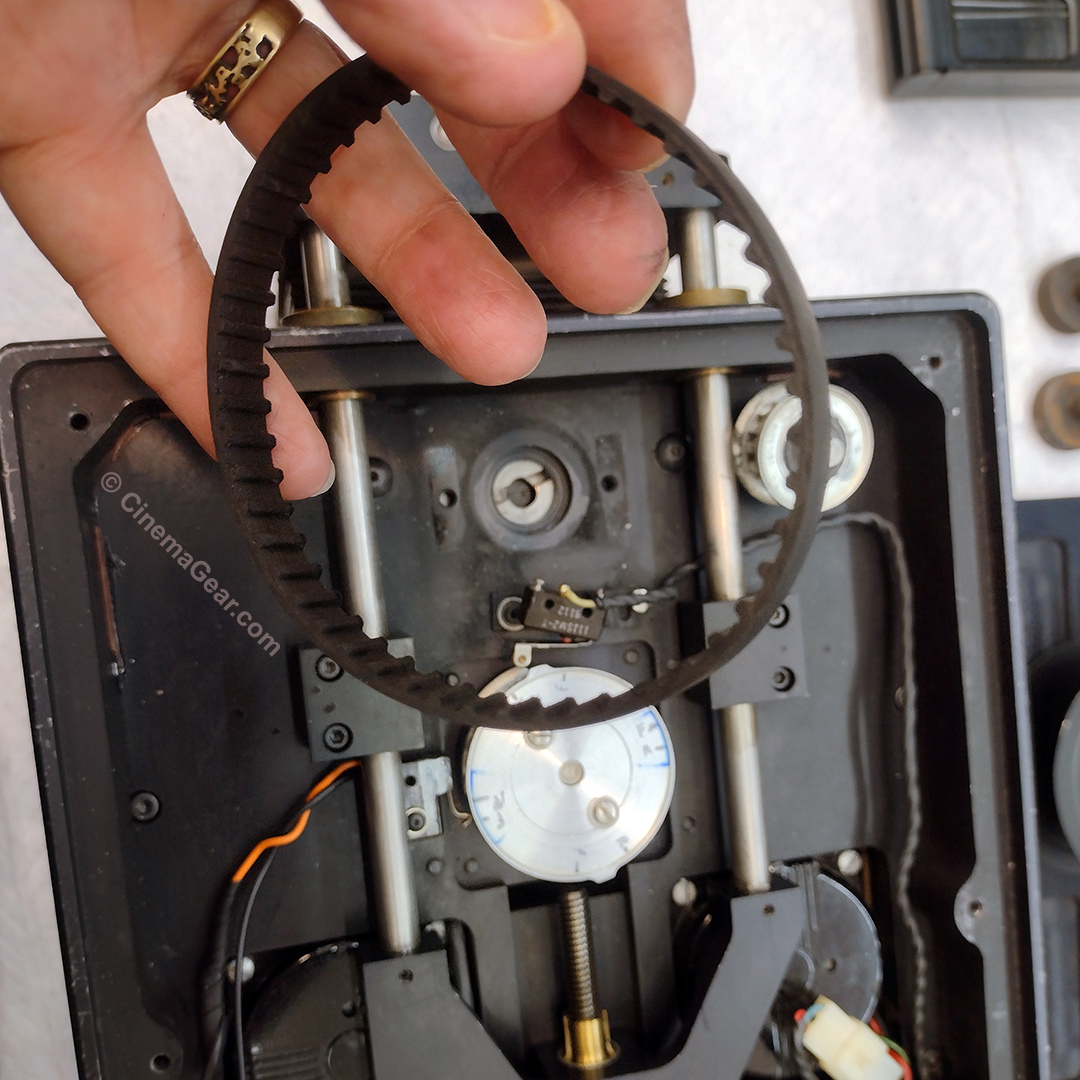
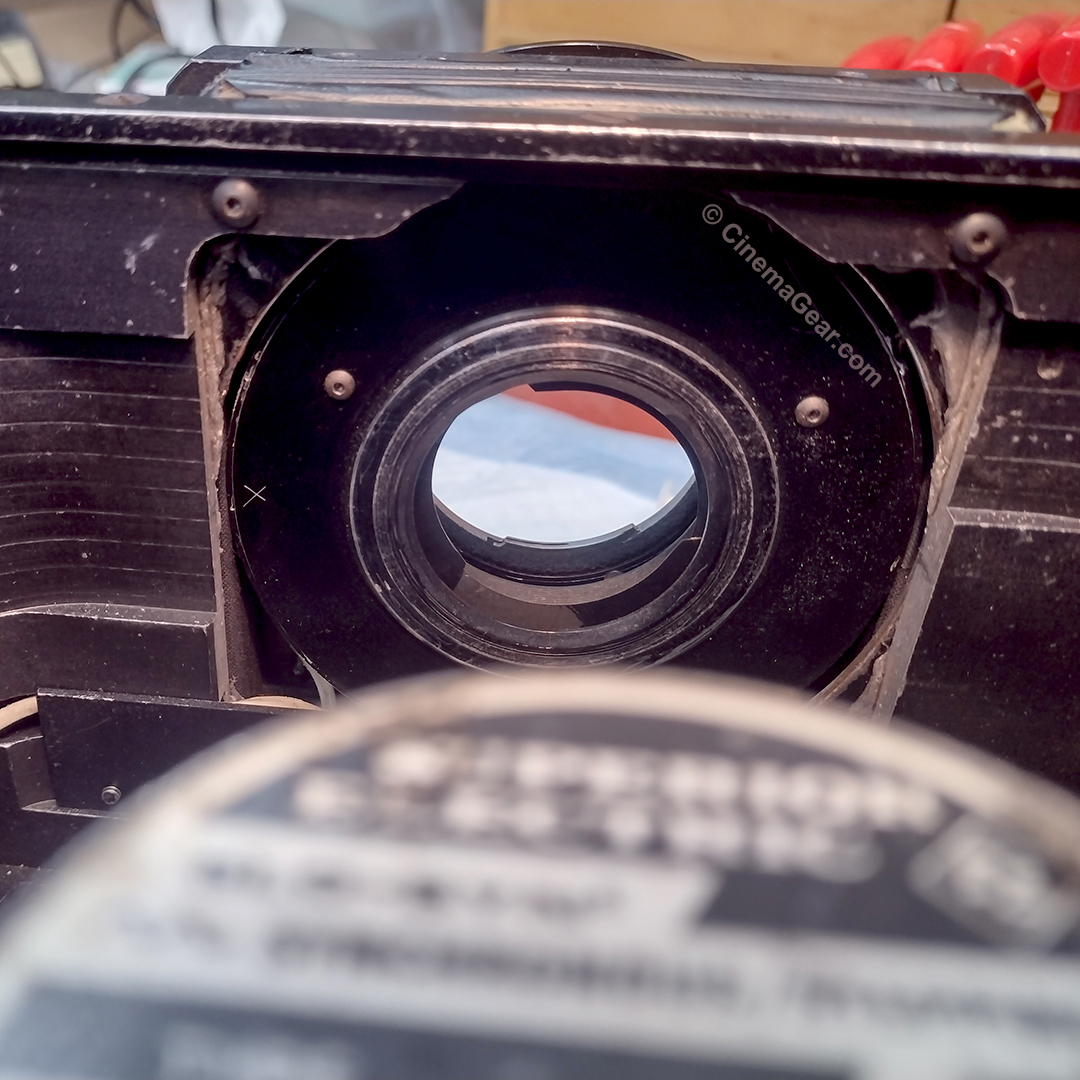
During my time servicing the Dykstraflex camera, I observed some interesting features and quirks and I thought it would be fun to share them briefly here. Unlike most of the cameras I worked with when I was shooting VFX, the Dykstraflex movement has a Vista Vision format ground glass mounted to it. The ground glass also features an animator’s field chard etched on it, a most useful feature. In the Mitchell cameras I used for VFX work, we had to punch film clips and slide them in the ground glass holder to do line-up. This seems to be a world better than that.
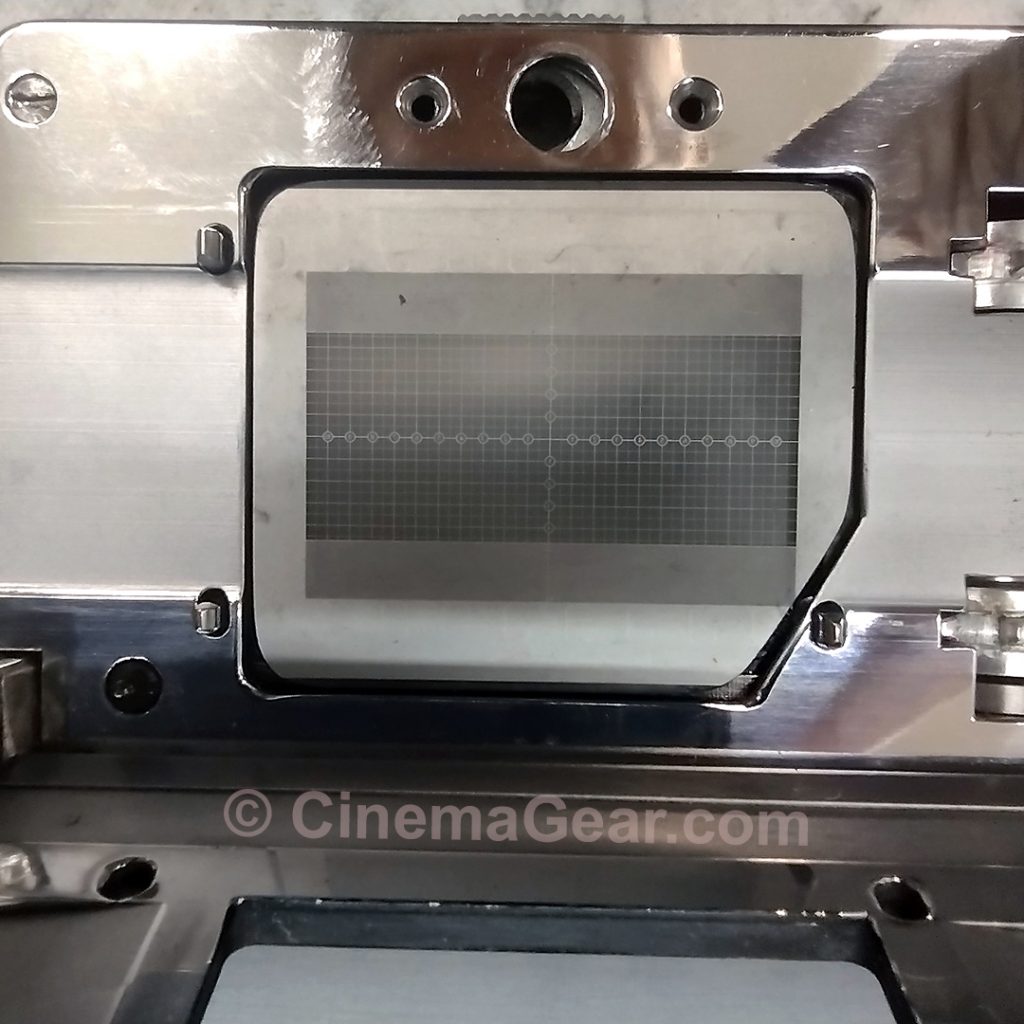
In the Dykstraflex camera’s original configuration, it used a rotary encoder. Looking at the configuration from the mechanical side of the camera, it looks like there was a rack gear bolted to the 3 elongated holes you can see on the lower left, which operated a gear on the rotary encoder drive shaft so that, as the follow focus mechanism moved forward and backward, it would update the encoder position. I would guess that this system talked to the motion control computer to keep track of focus, which once again was far superior to how the cameras I used worked. In the 2nd photo below, you can see the lead screw, the zero backlash nut, and the focus carrier plate that move the lens forward and back to follow focus.
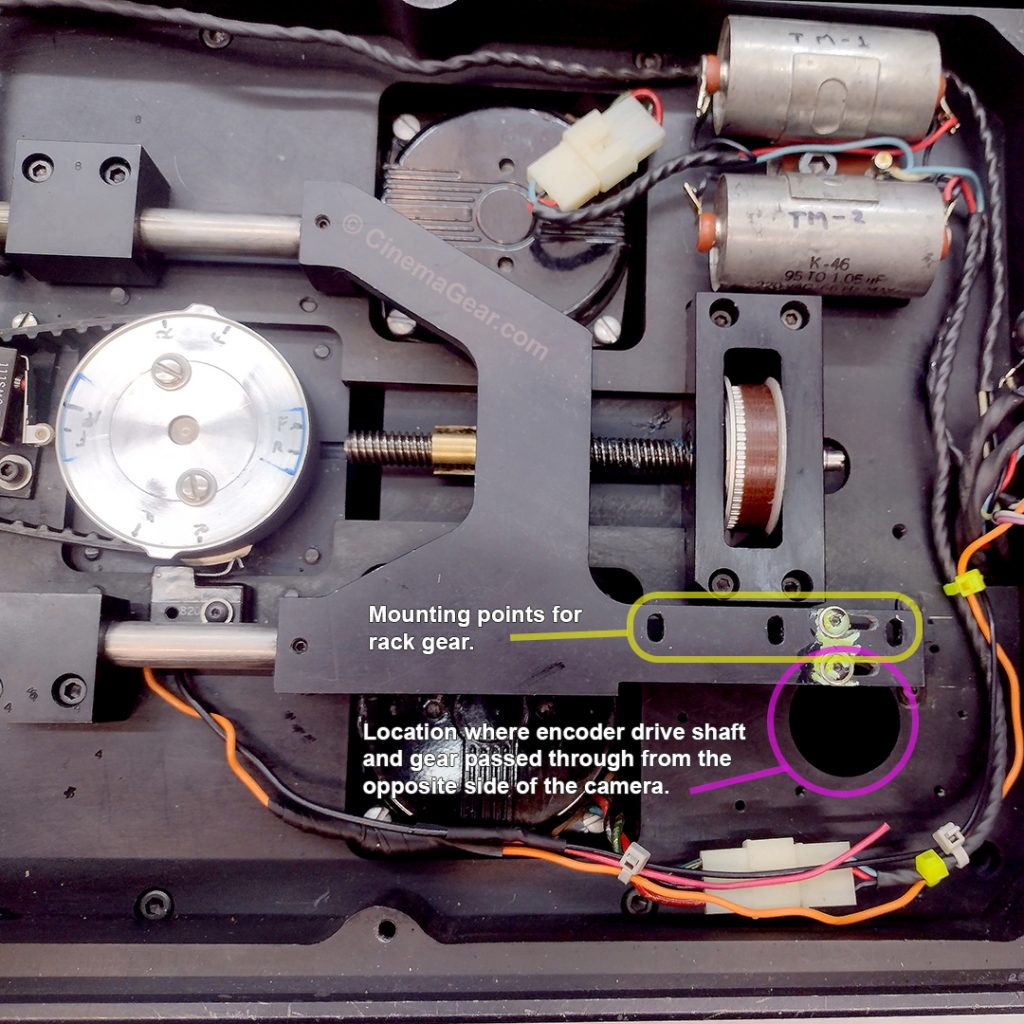
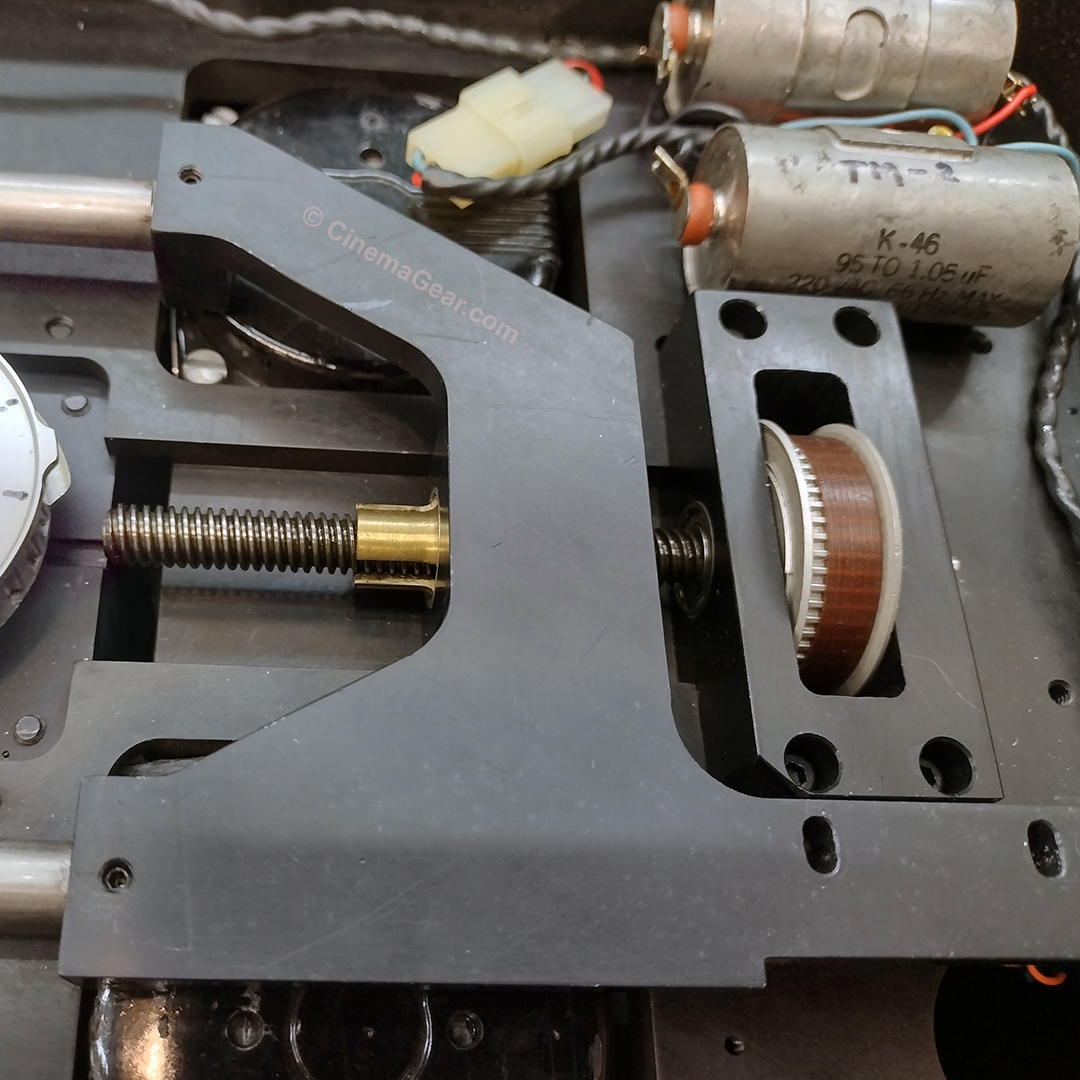
One of the quirks of this camera was how difficult they made it to change the belt on the follow focus. In order to achieve this, you have to remove the inching knob, unbolt the stepper motor from the camera, turn the camera over, remove the follow focus sprocket on the mechanical side, free the sprocket from the mounting assembly, and then finally remove the belt. Not an ideal arrangement.
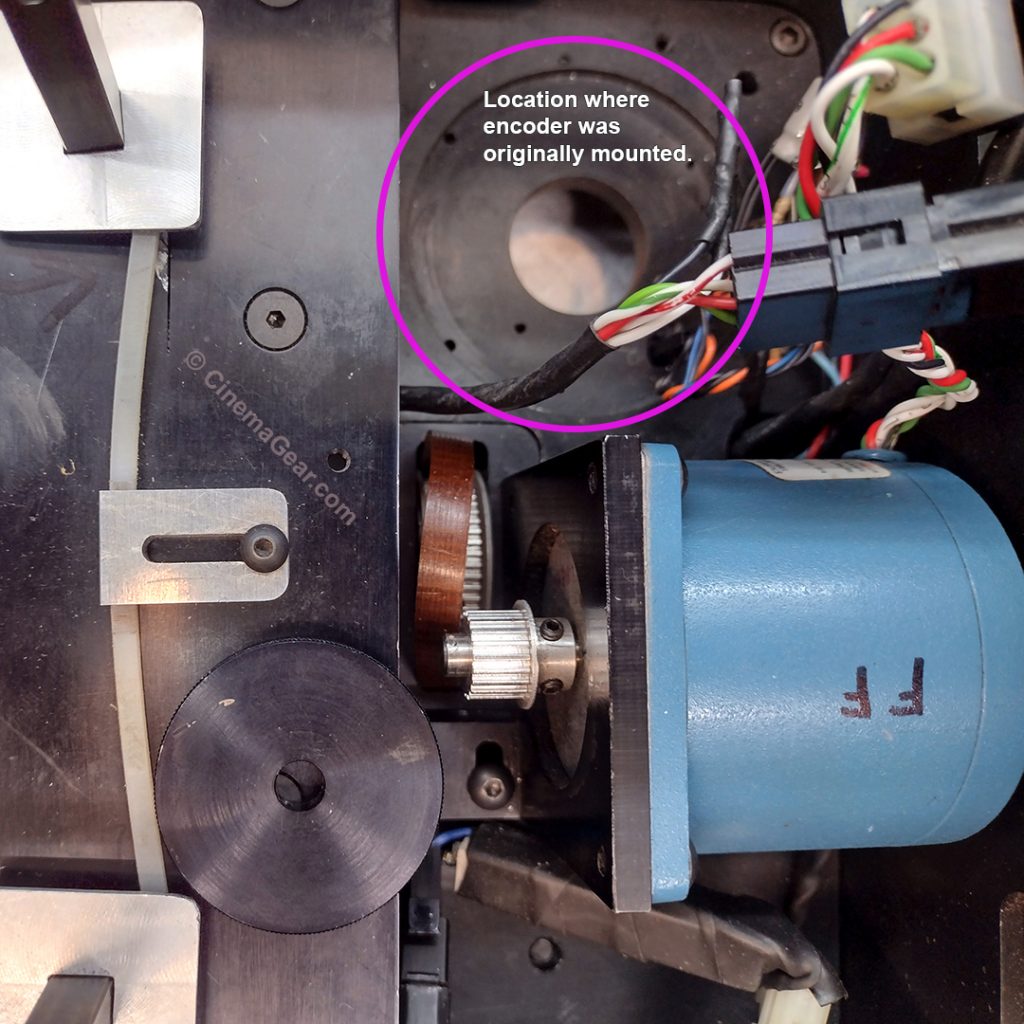
Sometime in the history of the Dykstraflex camera, the encoder was removed and cams and microswitches were installed on the movement drive sprocket. My guess is this was used to do some form of slit-scan photography so the computer would know where the apparent shutter open and shutter close positions were. The other quirk I found, whoever wired the microswitches for this function, ran the wires through the hold where the encoder used to be mounted. So, in an effort to be able to return the camera to its original condition, I rerouted those wires to a position where they wouldn’t interfere with the encoder should we ever decide to reinstall it (along with Richard Edlund’s pig nose sticker seen in many vintage pictures of the Dykstraflex).
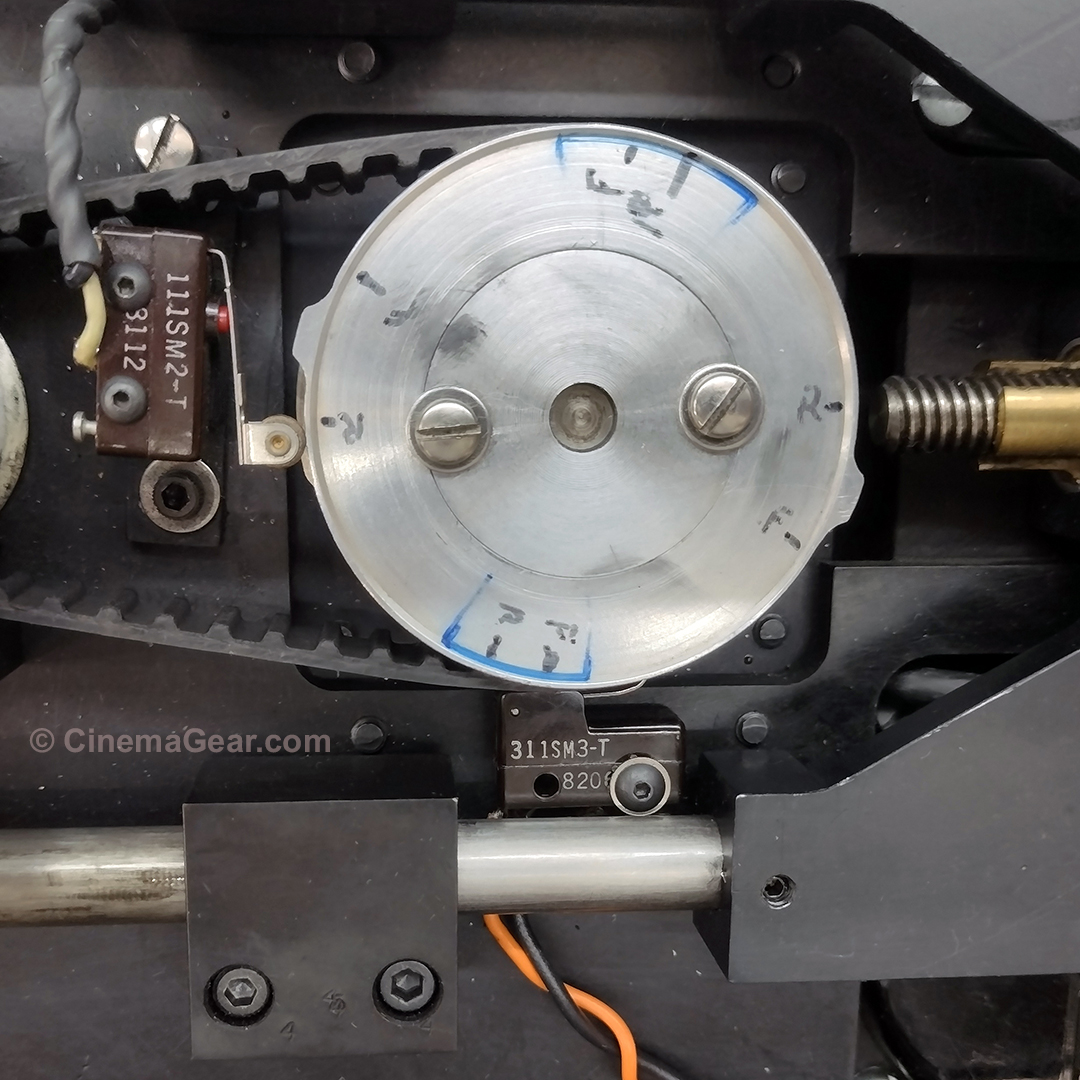
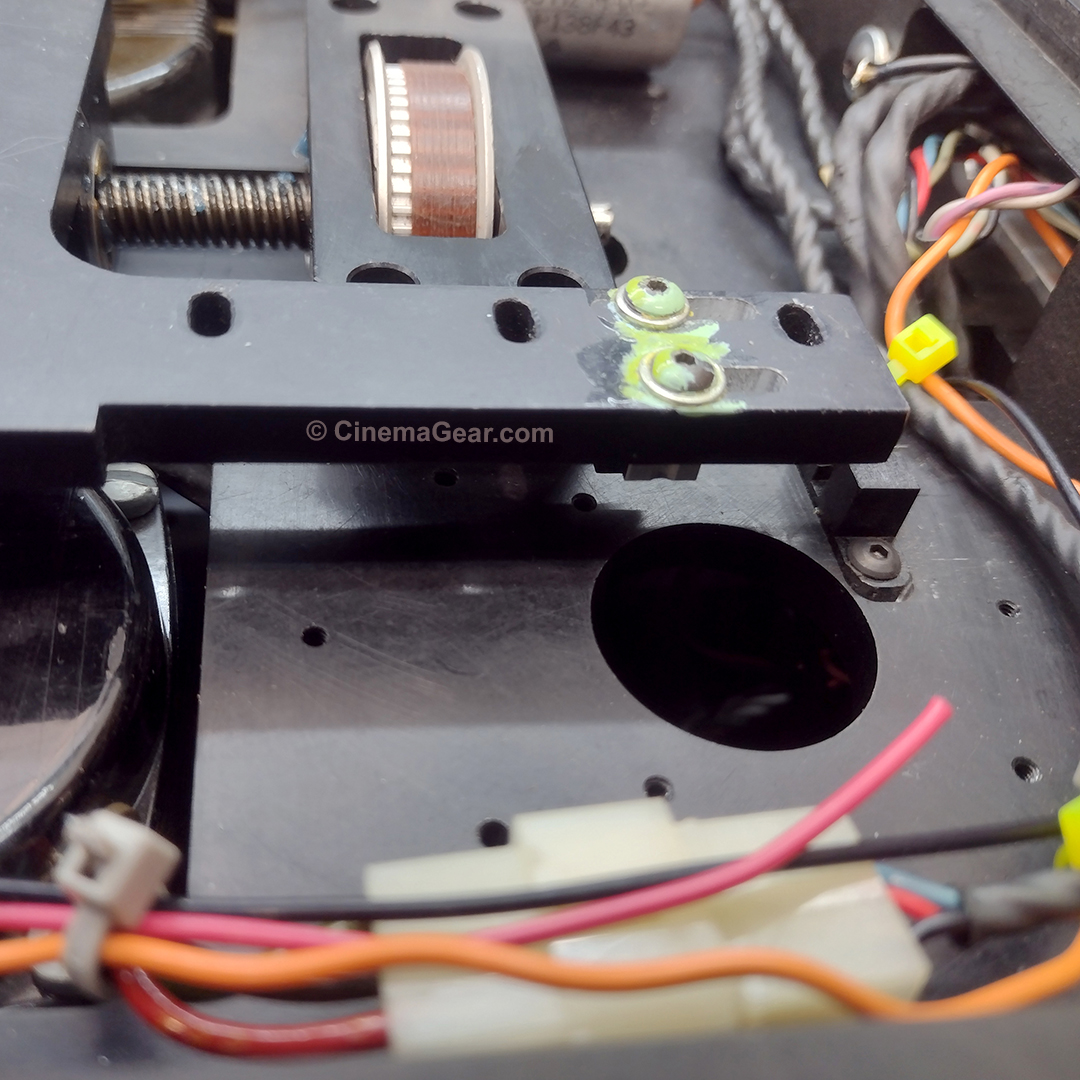
The Dykstraflex incorporated many clever and ingenious features that changed the dynamics of how on screen space ships could fly, among many other innovative visual effects. I was amazed at how well the camera had been stored and preserved, and was delighted to be involved in making it production ready once more.